Setki wieloosiowych systemów lutowniczych INERTEC z serii ELS są używane od 1993 roku w produkcji elektroniki na całym świecie. Te systemy lutownicze umożliwiają zautomatyzowanie praktycznie wszystkich aplikacji lutowania ręcznego. Jakość lutowania jest taka sama jak w przypadku systemów lutowania gazowego. System ten, preferowany przez wielu znanych dostawców usług elektronicznych, oferuje solidną konstrukcję i proste programowanie.
Bardzo szybka konserwacja jednostki lutowniczej, z której znany jest system, zapewnia pełną dostępność systemu nawet w trybie wielozmianowym.
Korzystając z systemu szybkiej wymiany dysz lutowniczych, urządzenie można zmodyfikować za pomocą zaledwie kilku ruchów ręki, aby poradzić sobie z najróżniejszymi zadaniami lutowniczymi. Precyzyjna kontrola wysokości i temperatury lutowania stanowi podstawę niezawodnej kontroli procesu wymaganej przez użytkownika.
Moduł lutowniczy, który jest dostarczany z dwoma jednoczesnymi lub autonomicznymi modułami lutowniczymi, zapewnia maksymalną dostępność technologiczną dla wszystkich produktów; duże złącza lub lutowanie punktowe - nie stanowią problemu dla tego systemu. Na życzenie dostępny jest również wymienny moduł lutowniczy i jednostka transportowa. Stosowanie lutów bezołowiowych jest obowiązkowe, a moduł lutowniczy jest emaliowany na całej powierzchni.
System lutowniczy ELS 3.3 został zaprojektowany z myślą o produkcji małych i średnich serii. Łatwe do zaprogramowania minifale z dyszami zwilżalnymi i przeciwprądowymi umożliwiają obróbkę dowolnego podzespołu przy użyciu zoptymalizowanych parametrów. Moduł lutowniczy jest wyposażony w sterowany osią system topnika i wielostopniowy system wstępnego podgrzewania ceramiki szklanej opracowany specjalnie do produkcji podzespołów.
Moduł lutowniczy jest wyposażony w sterowany osiowo system topnika i wielostopniowy szklano-ceramiczny system podgrzewania wstępnego opracowany specjalnie do produkcji podzespołów.
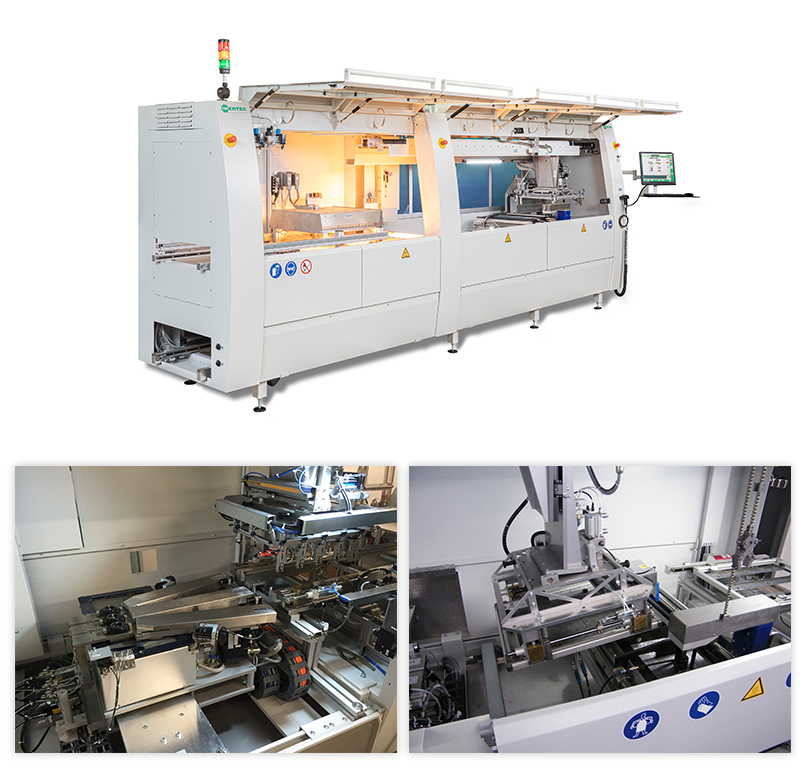
System lutowniczy ELS 3.3 został zaprojektowany jako centrum lutownicze do pracy w linii z podłączeniem do zewnętrznych systemów transportowych. W przypadku specjalnych zastosowań, jednostka lutownicza może zostać rozbudowana tak, aby tygiel mógł pomieścić do 4 fal równolegle.
Dzięki solidnej konstrukcji jednostki lutowniczej i profesjonalnemu systemowi osi X-Y-Z z serwonapędami, możliwe jest przetwarzanie detali o dużej masie. Możliwe jest zatem zintegrowanie tego z funkcjami wyrównywania i przytrzymywania chwytaka. Dzięki liniowej konstrukcji poszczególnych komponentów, topienia, wstępnego podgrzewania i lutowania, w systemie można przetwarzać 3 palety, a procesami można zarządzać niezależnie od siebie w sposób neutralny dla cyklu. W tym celu nad topielnikiem i systemem podgrzewania wstępnego zainstalowany jest łańcuch transportowy. Fala lutownicza o średnicy 40 mm może być używana do lutowania małych podzespołów.
Wybierz spośród wielu wymiennych dysz, aby dopasować się do specjalnych zadań lutowniczych. Mamy idealne rozwiązanie dla praktycznie wszystkich potrzeb związanych z lutowaniem.
Oprogramowanie ELS 3.3
ELS 3.3 Inline to idealne rozwiązanie, jeśli potrzebujesz elastyczności i wydajności. Inteligentne moduły lutownicze sprawiają, że wymiana dysz nie jest konieczna lub można używać kilku dysz lutowniczych równolegle. Może również pracować z 2 tyglami lutowniczymi zawierającymi różne spoiwa jednocześnie - można nawet użyć pełnej fali. ELS 3.3 wyznacza zatem nowe standardy w zakresie elastyczności i przepustowości.
Zwiększone wymagania jakościowe w sektorze motoryzacyjnym wymagają wykwalifikowanego procesu lutowania, z odpowiednią kontrolą procesu i identyfikowalnością partii - co jest oczywistą zaletą tego zautomatyzowanego rozwiązania. ELS 3.3 jest doskonale przygotowany - dzięki różnorodnym koncepcjom identyfikowalności, od prostego wykrywania kodów kreskowych po złożone połączenie z komputerem głównym.
Obecnie wydajność oprogramowania odgrywa znaczącą rolę. Jak szybko mogę wdrożyć mój projekt? Cóż, jeśli masz odpowiednie narzędzia... w mgnieniu oka. Offline - wygeneruj podstawowy program z łatwością, graficznie za pomocą miejsca pracy lub za pomocą plików Gerber. Już na tym etapie można zoptymalizować ścieżki procesu, obliczyć czasy cykli i uruchomić symulację. Następnie wystarczy dostosować parametry procesu na komputerze maszyny, aby dopasować je do płytki drukowanej - zadanie wykonane.